Raku ceramics firing: the technique coming from the east
Raku ceramics, linked to the oriental tea tradition, is experiencing a second life in these years. Raku ceramics objects are increasingly sought after by all those who love to have elements with a minimalist but refined design at home.
The art of raku ceramics is based on Zen philosophy. It is able to enhance the harmony of small things, the beauty of simplicity and naturalness of objects.
Linked to the tea ceremony, so dear to the Japanese people, raku ceramics was born in the early 16th century.
The true origin of this technique is not certain, but it is believed that its creation is due to a Kyoto ceramist who with this technique began to produce clay bowls. The particular composition of this material required the construction of a small raku ceramic kiln very particular for quick firing. These bowls had an unexpected success, so much so that the ceramist, in order to manage all the orders, had to cut the time and thought to extract his products still hot from the oven, thanks to the help of iron tongs. Thus the raku technique probably started.
Processing of raku ceramics
The peculiarity of the processing of raku ceramics consists in a firing process that takes place in a particular oven at temperatures ranging between 900 and 1000 degrees centigrade.
In order to obtain raku ceramic objects it is necessary to use a different type of clay from that used for classic creations. The refractory or semi-refractory one is generally used.
Here are the main steps that show how to make raku ceramics:
- Cook the object between 900 and 1000 degrees for about 3 hours
- Extract the still glowing piece with the help of long iron pliers
- Place the object in a container full of easily combustible material (wood shavings, newspaper sheets, sawdust). The contact of these materials with the incandescent ceramic causes the ignition of a flame that burns all the fuel present in the container
- Immerse the piece in the water
- Clean the object to eliminate the signs of the combustion that has just occurred
This technique causes chemical and physical transformations of the object. First of all, a large reduction (partial or total) of the volume due to the elimination of the air particles inside it. The type of reduction obtained can be seen from the color of the clay: the black ceramic is due to a total reduction while depending on the amount of oxygen left the color will change on the gray scale.
To choose the type of reduction you want to obtain, you need to consider several factors such as the fuel used, the burning time, the total or partial coverage of the object.
The raku technique today
The raku ceramics working technique was brought to the western world in the early 1900s by Bernard Leach, an English ceramist who spent about ten years of his life to deepen the techniques of the master potters of the Far East.
The diffusion and success of raku ceramics in the west began about forty years ago, in particular in the Anglo-Saxon world (Great Britain, United States, Australia), following the dictates of the reduction technique to have objects with unique design and colors.
The basic technique remains the same, but new technologies are used allowing optimal “management” of the entire manufacturing process.
Objects that can be made with raku ceramics
Thanks to this particular technique, the design objects that can be made following the processing of raku ceramic can be different and belong to different areas. Specifically, we refer to:
- vases and bowls
- design or fantasy objects
- statues
- panels
- jewelry and necklaces
Raku ceramic glazes: Sicer protagonist of excellence
Raku glaze is par excellence one of the oldest products in the history of ceramics and Sicer, always attentive to both tradition and innovation, among its products it holds a series of raku glazes with shiny and satin metal surfaces that allow to achieve unique and exceptional aged effects.
Everything comes from the desire and curiosity to transfer the effects and surfaces of the ancient Raku ceramics onto ceramic tiles, which have always been present in our homes with unique and unrepeatable design objects.
Modern technology allows us today to apply this special glaze on both flat and textured surfaces, directly on biscuit or on vitrified glass through the use of airbrushes or traditional screen prints.
The decorative effect obtained with metallic reflections and crazing make the raku technique extremely original, distorting the classic method.
However, the maximum splendor is achieved by working the raku glaze together with reactive glass of “old generation” (such as the lacquer series and the craquellè series) or with avant-garde glass like the Murrine-Shadow and Vulcano-Titanium series, applicable both wet and dry.
From these material combinations originate always refined particular surfaces and unique materiality.
Here are some examples that show the final result after applying Sicer raku glazes:
- On pressed biscuit, a glazing of raku glaze in warm and cold tones with material enrichment, thanks to the dry application of reactive glass from the Shadow Series.
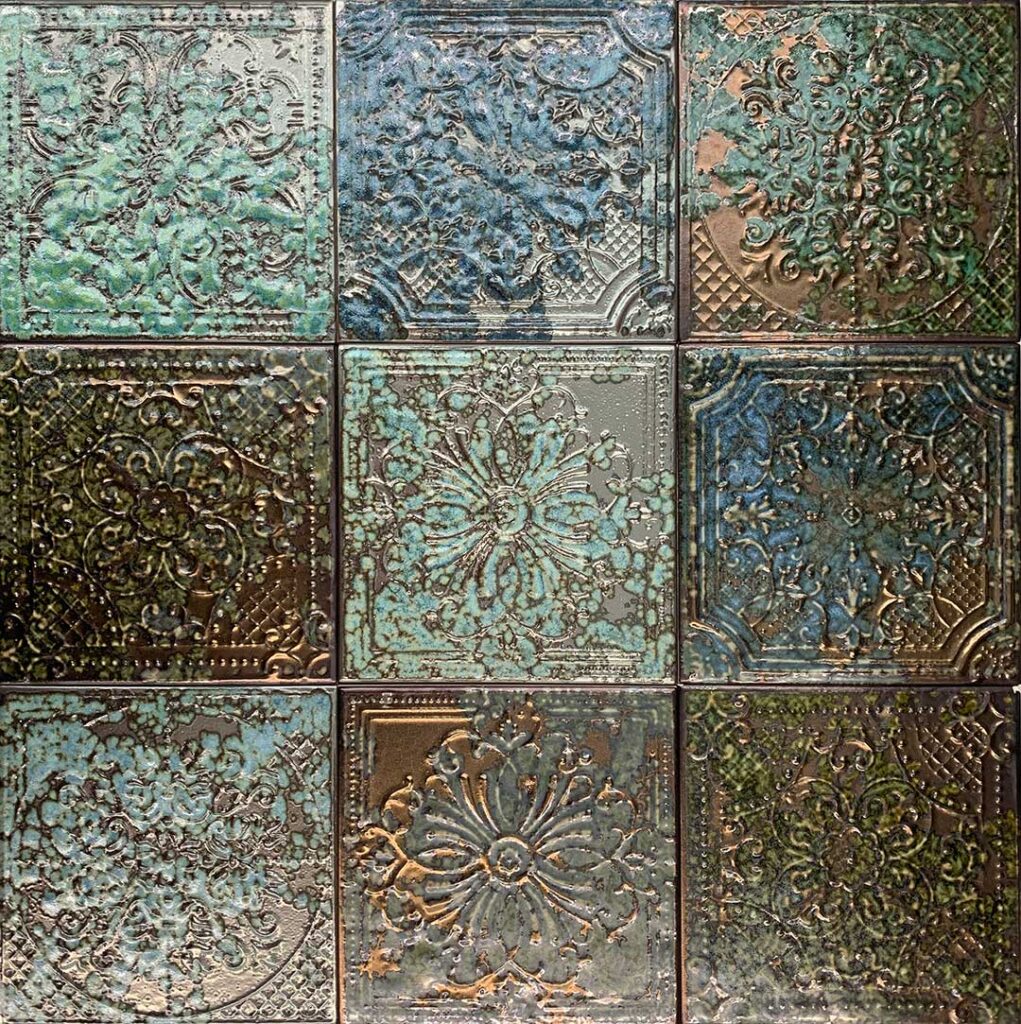
- A mix of reactive glass (murrina, shadow, craquellé) applied dry on a raku glaze base applied by screen printing. Material combination between traditional and new generation products.
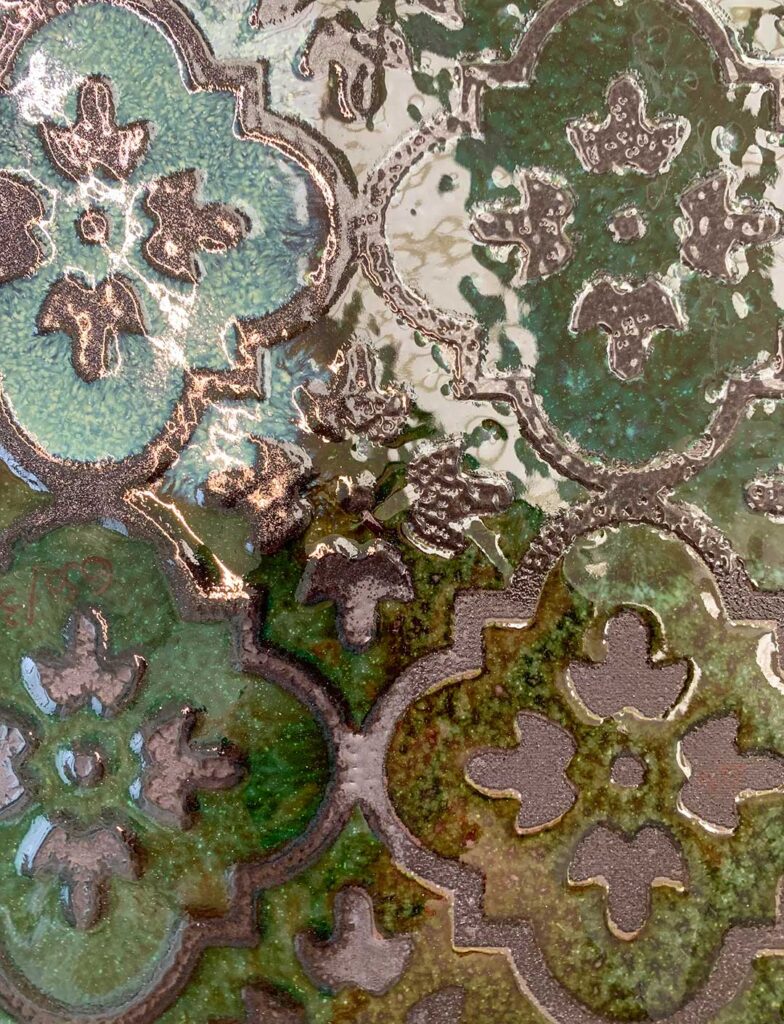
Colors for raku ceramics
he DBU, Decoration Business Unit, of Sicer has created particular shades suitable for third firing ceramics, as well as a special base for Raku. The latter allows to obtain a better result in terms of hold and color result.
The colors for raku ceramics available are:
- Raku light steel
- Bronze Raku
- Platinum Raku
- Raku steel
- Blue raku
- Gold raku
- Raku lemon gold
- Raku matt lemon gold
- Pewter Raku
- Brass raku
As the main partner of the ceramic industries, Sicer, which gives importance to modern Italian art, wanted to add glazes dedicated exclusively to the raku ceramics technique to have a complete offer and give decisive support to its customers. This type of processing (niche, but refined) with the use of ad hoc glazes allows the creation of particular, unique and exclusive objects.
The important return to color of recent times has pushed Sicer to interpret and propose raku glaze as a metallic finish on basic colored serigraphs, thus giving a real added value to what has been replaced for years by digital printing only.
In this regard, it can certainly be concluded that digital ink printing on raku glaze allows to obtain shadows and three-dimensional effects difficult to reproduce with other types of glaze, making this technique truly unique.
Discover the products
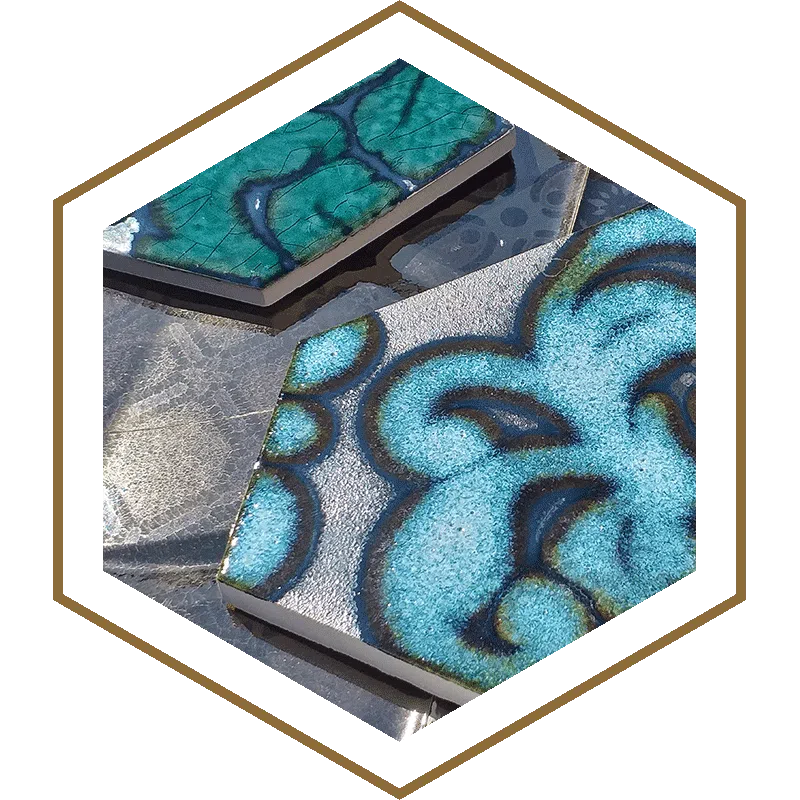
Raku glazes
LearnFrequently asked questions
Raku ceramics is a Japanese firing technique characterised by manual processing and a rapid cooling phase, which creates unique aesthetic effects such as metallic reflections and irregular textures.
Specific Raku glazes contain metal oxides and special pigments. The special feature of these glazes is that they create metallic effects in a single firing at high temperature.
The main steps include shaping, the first firing (bisque), application of the glaze and a second rapid firing. After firing, the piece is quickly cooled in a reductive environment (often sawdust or dry leaves) to create the characteristic reflections.
The most common effects include metallic reflections, craquelé surfaces (with small cracks) and iridescent colour combinations due to the reaction of metal oxides during firing.
Raku ceramics differs from traditional techniques due to its fast-firing method and immediate cooling, which creates unique and unpredictable surfaces.