Today, thanks to the several application and use possibilities, ceramic grits are one of the most versatile and interesting product families in the whole ceramic sector. Sicer currently produces a wide range of grits and micro-grits in all its production plants, both in Italy and abroad. Their quality, result of constant research, allows the world’s leading ceramic manufacturers to differentiate their products and achieve unique performance compared to other materials on the market.
In this article we will talk about what are the grits, how they are produced, what are their main applications and we will see, in detail, the technical characteristics of the grits developed by the laboratories of Sicer, historic manufacturer and supplier of raw materials for ceramic companies and reference partner of the best ceramic groups in the world.
What are the ceramic grits
Ceramic grits are glass matrix materials that are applied to ceramic tiles to give aesthetic, structural and sometimes protective effects to the ceramic surface itself. The main advantages are hardness and high wear resistance.
How are produced the ceramic grits: from frits to grits
Frit is a semi-finished product that needs to be transformed into calibrated grit to be used in the ceramic production process.
The production of grit requires a grinding stage using rollers in order to reduce the average size of the glass granules. At this stage, it is also necessary to calibrate the particle size distribution suitable for use in ceramic decoration with modern production processes. That is why it is necessary to proceed with a sieving process by means of a battery of vibrating sieve that allow to obtain different fractions of grit with controlled particle size distribution.
The number and type of sieves and the operating parameters of the plant determine the final particle size distribution of the finished product.
Each lot of grit produced is methodically checked by Sicer’s Control Laboratory in Torriana, in order to verify the characteristics of the product. Among the different parameters controlled by way of example there are: the characteristic temperatures by heating microscope, the dimensional distribution by means of vibrating sieve and laser particle size, the presence of any impurities by ceramic tests.
Sicer has an extensive catalog of grits with different properties. It is therefore possible to make mixtures of grits that combine the different properties and exploit synergistic effects. The use of a mixture allows to optimize the aesthetic and technical properties of the grits such as color development, transparency, the matt level, the coefficient of expansion and chemical attackability. Other properties such as the laying of the glass layer and the residual porosity at the oven outlet can be modulated in order to maximize the effectiveness and efficiency of the eventual subsequent lapping of the tiles/slabs. Here too, mixtures undergo an extensive programme of checks, similar to the one described above, in order to guarantee the quality of the product.
How ceramic grits are applied
Today, ceramic surfaces are mainly produced by wet or dry application of grits.
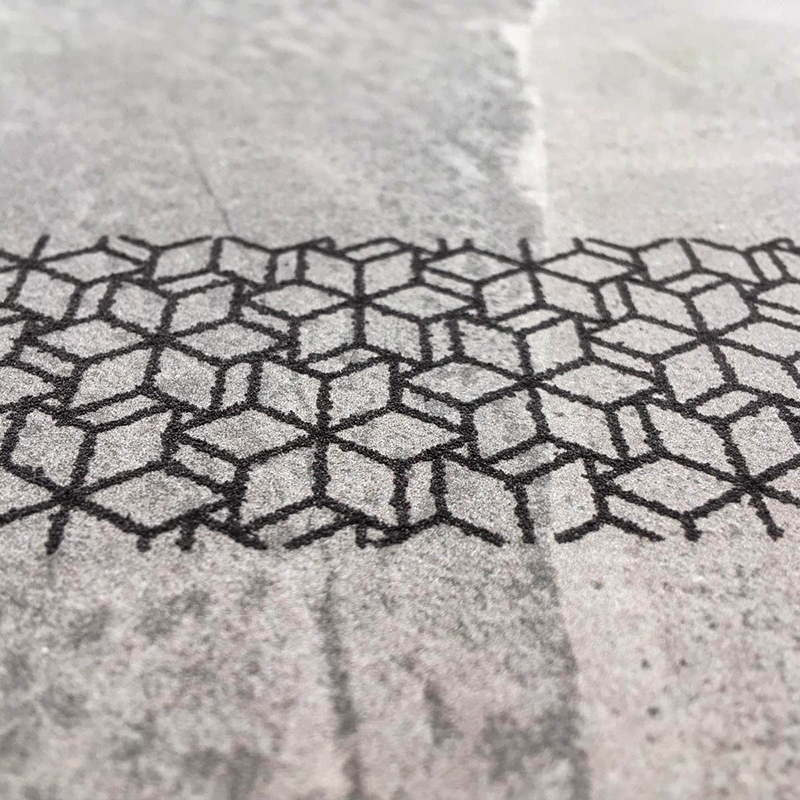
Before the advent of digital, the application of the grit on the entire surface of the ceramic tile could be done dry, by blasting, following the application of glue with airbrush or similar machinery, or wet with glue and grit application together in a single liquid compound applied to airless.
The application of the grit to drawing, was by application of the glue by screen printing on a predetermined image.
In recent years, however, the main OEM (Original Equipment Manufacturer) of the ceramic industry have developed machines able to deposit glue with digital technology, with the advantage of being able to apply it with maximum precision only in predetermined areas (also very small areas) and consequently to adhere the grit applied above only on the details required by the graphic setting.
Let’s see in detail these different types of application.
Dry application of grits
Ceramic grits can be applied dry by shot blasting applicators.
Thanks to this method, more marked textures of the ceramic surfaces are obtained and a greater quantity of material suitable for mirror sanding can be deposited.
The dry technology implies a preventive application of glue, digital or airless, and a possible second application of a low weight of fixing glue, once the grit has already been laid and glued on the support.
A process, therefore, that develops in three phases, that is:
- Application of the glue
- Application of the dry grit
- Possible application of a low glue weight
The application method described above offers both technical advantages and environmental advantages.
The technical advantages include:
- Improved transparency and compactness of polished glass
- Easier application of grits with greater grain size
- Possibility of applying substantial quantities of grit
- Possibility of obtaining decorations with thickness
Among the environmental benefits, the most important refers to the significant decrease in water use:
- The grit is not suspended and therefore the liquid part is substantially non-existent.
- The amount of glue previously applied is very small.
This is reflected in energy consumption which is inevitably lower with less impact on the surrounding environment.
Wet application of the grits
In ceramic, the application of vitreous grits can be wet either as a spray using an airless sprayer, or a veil using a bell or waterfall unit. Methods that involve the use of aqueous systems in which the grit is suspended.
The application of grit suspensions in liquid glaze and organic additives allows the homogeneous and constant deposition facilitating the control of the production process and the quality of the ceramic surface after firing.
In wet application it is possible to use single grits or mixtures of fine-grained grits and this allows to obtain smooth ceramic surfaces and excellent application even for the rougher structures.
Thanks to the wet application it is possible to obtain different types of ceramic surfaces, from the polished to the sugar effects, up to the non-slip textures and high abrasion resistance.
The main technical advantages offered by the application of wet microgrits are:
- No creation of dust
- Less consumption of grit being a suspension
- Complete homogeneity of the mixtures of the different grits
- Distribution on the surface of the tile uniform and smooth
Digital application of the glues
Thanks to the digital application of the glue, today grits can also be used to create drawings or relief graphic details very defined and particular.
By digitally applying the glue only in the predetermined areas and in line with the underlying graphic design, the grit applied subsequently dry, adheres only in the required areas and the result are sought-after and detailed effects. The digital glue also allows to apply the dry grits also on the entire surface of the tile in a very precise way, giving a very high uniformity of application even for mirrored lapping, without any defects.
Water based digital glues: why choose a water based digital glue?
The latest series of Sicer digital glues is the new range of water-based digital glues. These glues, in addition to being ecological and with very low environmental impact, allow a better management of high, medium and low quantities of grit. But why? The combination of the two components of the water-based digital glue forms a gel, which minimizes the part of glue absorbed by the support allowing a precise adhesion of low, medium, high quantities of grit.
Water-based glues, unlike solvent-based glues, exploit more the incompatibility with the underlying graphic (also solvent-based), remaining more floating on the surface, and ensuring the grip of grits in high or low quantities, depending on the exhaust control.
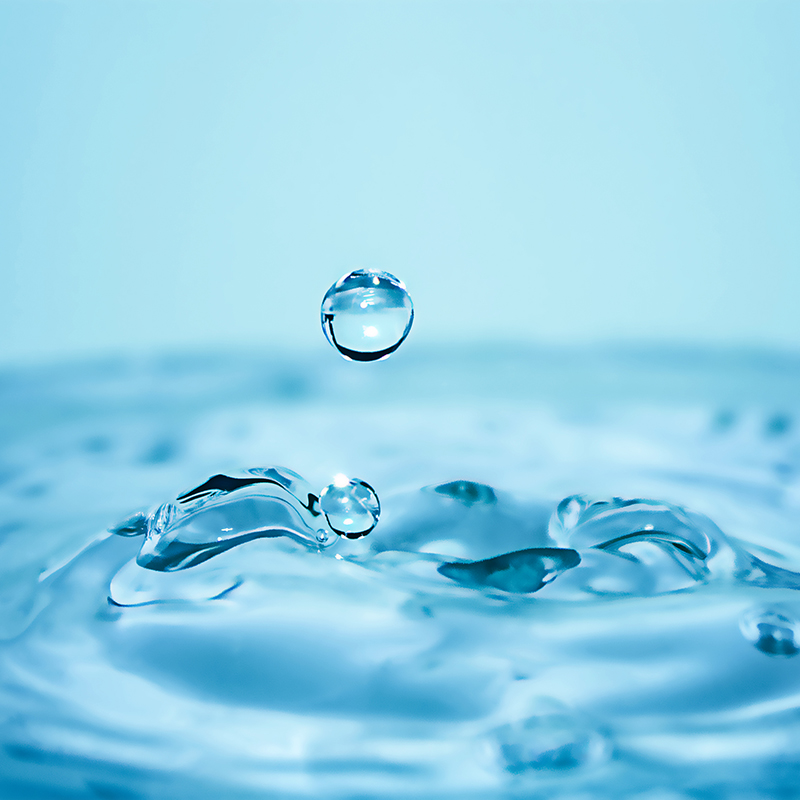
Advantages of using water-based glues:
- improved application process in production line
- more creative possibilities in the development of the ceramic project
- very high adhesive power (the clinging of a high amount of glass, creates an important thick effect)
- totally odorless and low emission
All Sicer water-based glues guarantee higher drying times than common solvent-based glues.
Technical grits and microgrits by Sicer
Sicer produces a wide range of technical grits and microgrits and their excellent quality is the result of the know-how that characterizes the constant research and production processes.
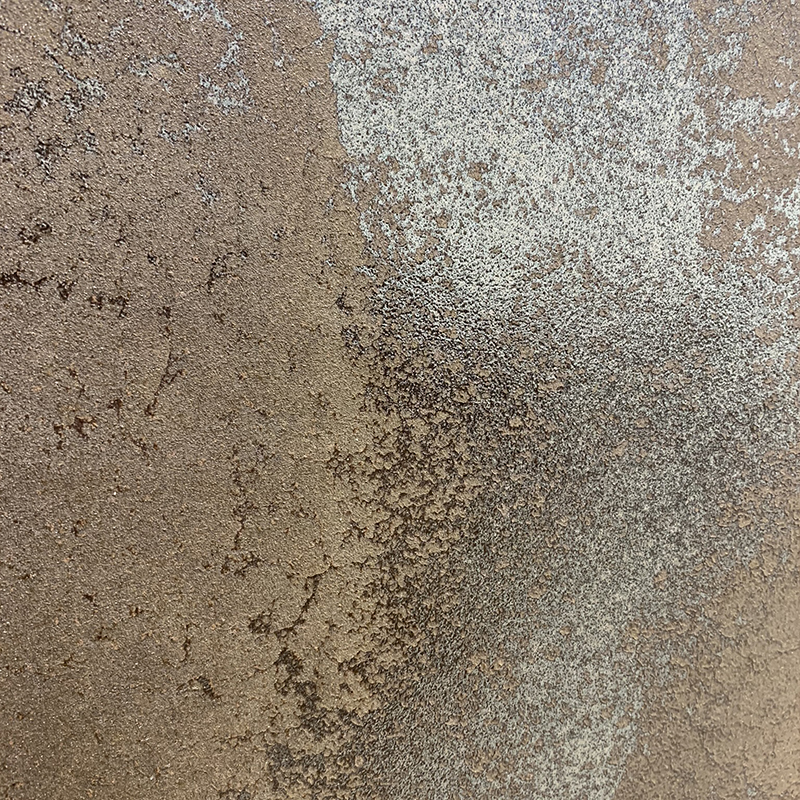
Sicer’s range of grits and micro-grits consists of the following products.
GHR grits
The series of GHR technical grits allows to realize a wide range of natural surfaces, pleasant to the touch and anti-reflective, ensuring an excellent development of the color of digital graphics, an innate naturalness and wear resistance.
GRA grits
GRA neutral grits are characterized by the materiality of the product that allows individual use or customization through mixtures and different effects.
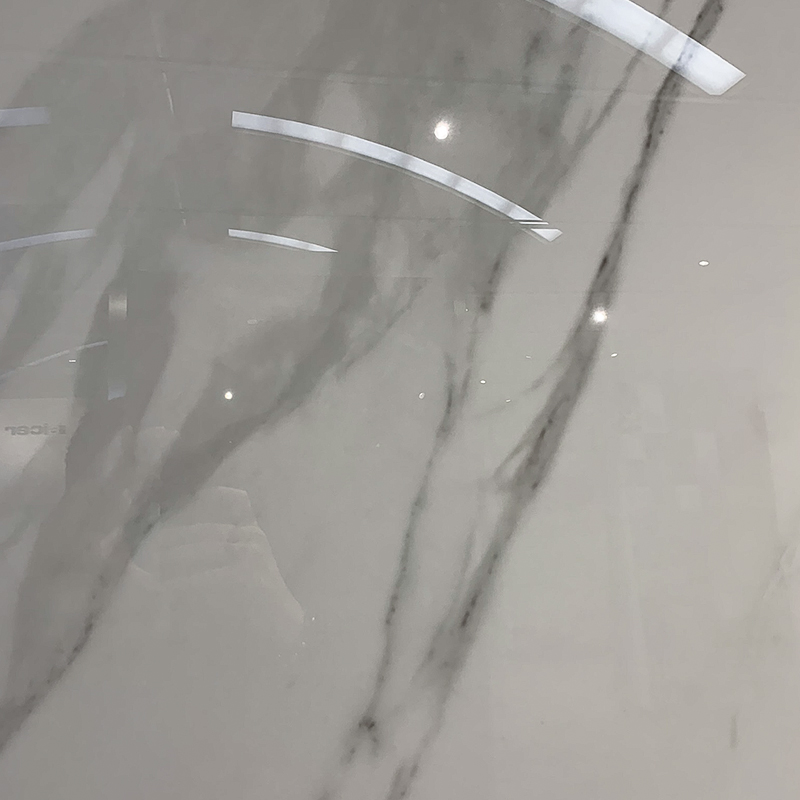
GRA-DRY LUX grits
The exclusive series of GRA DRY-LUX grits was born for the realization of mirrored lapped surfaces with dry application of grit on digital glue. These are perfectly transparent and compact grits, designed to ensure very bright surfaces such as marble, with a precise coefficient of expansion, no porosity and incredible depth of the glass.
GRAN LUX grits
GRAN LUX is a series of grits for wet applications for mirrored lapping. GRAN LUX supports the GRA DRY-LUX series for dry application and completes the range of grits designed to obtain ultra-bright, transparent, compact and non-porous lapped surfaces.
GRC grits
GRC series of coloured grits can be used individually or in combination with other GHR or GRA series grits. The colouration is in fusion or in mass.
GRS grits
GRS series presents grits, offered in different grain sizes, having different effects, among which: GSM metallized special grits, GRT titanium reactive grits and GRS special grits.
The wide range of grits and microgrits offered by Sicer allows to obtain multiple solutions able to meet every need of the market. The grain sizes are countless, selectable according to the application technology used and the desired result. Alone or mixed together, these grits can be used to develop different types of products, including: mirror finishes, cements, stones, sugar effect, decorated metallized and anti-slip surfaces, both indoors and outdoors.
Sicer: unique and personalized creations
Frequently asked questions
They enhance the aesthetic appearance, imparting effects such as gloss and texture, and increase the hardness and strength of ceramic surfaces, making them more durable and suitable for indoor and outdoor use.
Grits can be applied dry or wet, offering versatility in production. Advanced technologies, such as digital application, allow for accurate decorations on complex surfaces, guaranteeing unique and customised results according to the desired design.
This technique reduces water and energy consumption during processing. It also produces less waste and dust, contributing to more sustainable processing, in line with environmental regulations and the ceramic industry’s focus on sustainability.
Grits allow you to obtain extremely varied surfaces, such as mirror effect glossy finishes, non-slip textures for safe environments but also extremely pleasant to the touch for interior finishes.
Water-based digital glues are an environmentally friendly and safe solution. They enable precise application of grits, improving the quality of the final product and increasing creative possibilities in design.