Index
- Introduction
- Analysis of ceramic raw materials
- Industrial transformation processes
- Firing: definitive transformation of properties
- Glazes and vitrifying materials: the artificial contribution
- Technical classification: natural, artificial, or hybrid?
- Environmental aspects and sustainability
- Contemporary innovations in the sector
- Sicer technical granules: the engineered contribution to ceramic surfaces
- Scientific conclusions on the nature of ceramics
- FAQ
Introduction
The classification of materials as “natural” and “artificial” is a key issue in materials science, but also an ambiguous area when it comes to processed materials such as ceramics. In technical terms, a natural material is a substance found in nature without substantial modification (such as wood, stone, raw clay), while an artificial material is obtained through chemical synthesis processes and does not exist in nature (such as polymer resins or plastics). Between these two extremes lies an intermediate category: processed materials, i.e., natural materials modified by industrial processes, but without a complete molecular recombination.
Ceramics—in all its forms, from traditional tiles to technical ceramics—defies a single classification. Although its raw materials are natural, the processes it undergoes (grinding, mixing, pressing, firing at extreme temperatures) transform it so radically that it becomes a new material with structural, chemical, and optical properties that are profoundly different from those of the original materials.
For professionals in the ceramic sector – particularly R&D managers and laboratory technicians – understanding the hybrid nature of ceramics is not just an academic question. It is a starting point for:
- choosing the right formulations based on the type of use required (indoor/outdoor, technical/aesthetic);
- developing new decorative or functional solutions;
- assess the environmental impact of production processes and the materials used;
- position the product correctly on the market, including from a regulatory and sustainability perspective.
In this article, we will take a scientific and technical approach to analyzing all the stages that lead a natural material to become an advanced ceramic product, assessing the implications for classification and application. This will provide useful insights into where ceramics stand today in the contemporary materials landscape.
Analysis of ceramic raw materials
Natural origin
The main ceramic raw materials (clays, feldspars, kaolin, quartz) come from rocks of natural origin. They are formed by geological processes over thousands of years and are heterogeneous mixtures of aluminum silicates, often accompanied by mineral impurities that influence their technical behavior.
Chemical composition
These materials have variable compositions:
- Clays: hydrated, plastic, and refractory aluminosilicates
- Feldspars: alkaline fluxes, facilitate vitrification
- Quartz: inert, regulates shrinkage and thermal expansion
The chemical nature is key to understanding reactivity during firing.
Natural variability
The same clays can change color, plasticity, or oxide content depending on the quarry, geological deposit, and grain size.
Industrial transformation processes
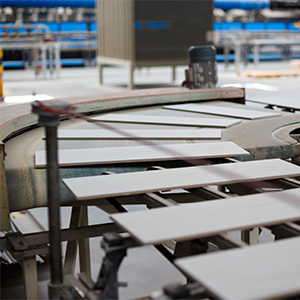
Preparation of raw materials
The first step in ceramic production is the preparation of raw materials, a phase that requires precision and control. The raw materials—mainly clays, feldspars, quartz, and kaolin—undergo a cycle of mechanical crushing and subsequent micronization to obtain a controlled and reactive particle size. This step is crucial to ensure uniform particle distribution, reduce the presence of impurities, and optimize chemical-physical reactivity in subsequent steps.
The powder obtained is then mixed in wet or dry plants, often with the addition of additives or organic binders, in order to improve its rheological properties and pressability. The aim is to obtain a homogeneous, stable and easily workable mixture that can guarantee consistent performance throughout the production line.
Forming
Once prepared, the mixture is transformed into a semi-finished product through various forming techniques, chosen according to the type of product desired:
- Pressing: the most common in tile production, involves the use of hydraulic presses that compact the powder into molds, obtaining slabs with uniform density and precise geometries.
- Extrusion: used for continuous section products such as klinker and strips, it allows plastic mixtures to be shaped by pushing them through a die, which is useful for complex shapes or hollow structures.
- Casting: used for complex products such as sanitary ware, it exploits the castability of fluid mixtures in porous molds that absorb water and leave a solid residue adhering to the desired shape.
Each method affects the mechanical and thermal behavior of the material, making the choice of forming technology a strategic aspect depending on the intended use of the ceramic product.
Drying
Once forming is complete, the raw product (also known as “green”) undergoes controlled drying, with the aim of eliminating the free moisture present in the mixture. This step is essential to prevent internal stresses and cracks that could compromise its integrity during firing.
Drying takes place in special ovens or hot air tunnels, and its effectiveness directly affects:
- residual porosity
- dimensional shrinkage
- initial mechanical strength
Parameters such as temperature, air speed, and duration are calibrated according to the composition of the mixture and the shape of the piece.
Pre-firing physical transformations
During these stages, the raw materials gradually lose their original characteristics. Clay, for example, transforms from a plastic and malleable material into a rigid and fragile body, ready for firing.
Physical and mechanical transformations include:
- structural changes in the clay matrix
- particle orientation during pressing
- the onset of surface sintering phenomena in the presence of additives
At this point, the material is no longer simply the sum of its raw materials, but a pre-engineered technical system, ready to undergo the final, crucial metamorphosis: firing.
Firing: the final transformation of properties
Firing represents the point of no return in the ceramic production cycle: it is the moment when the material passes from a raw and unstable state to a solid, coherent, and definitive state. This occurs through a series of chemical, physical, and structural transformations induced by heat, which transform the ceramic material into something completely new compared to the sum of its original raw materials.
Chemical reactions during firing
During firing, which typically takes place between 1000 °C and 1250 °C, depending on the composition of the mixture, numerous thermally induced reactions occur:
- Dehydroxylation of clay: clays lose structural water, transforming from phyllosilicates into more stable amorphous phases.
- Partial melting of fluxes (e.g., feldspars): these components begin to liquefy, forming a glassy phase.
- Sintering: the solid particles weld together, reducing porosity and increasing mechanical strength.
- Crystallization of new phases: such as mullite (3Al₂O₃·2SiO₂), which is formed by reactions between kaolin and silica, giving high mechanical properties and thermal resistance.
These reactions transform the ceramic body into a heterogeneous structure, composed of glassy and crystalline phases, which define its final properties.
Structural and optical variations
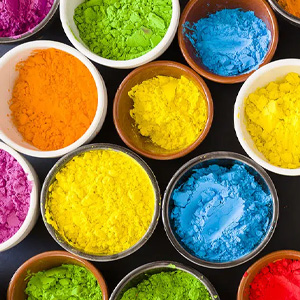
At the microstructural level, firing determines:
- reduction in porosity (from >10% to <1% for some technical stoneware)
- dimensional stabilization
- color development through the interaction between coloring oxides and the glass phase
- variations in reflectance and transparency
Once fired, ceramic material becomes inert, hygienic, mechanically stable, and resistant to chemical and atmospheric agents. It is this stability that makes it suitable for applications in industrial, public, or outdoor environments.
Impact on technical behavior
The technical characteristics resulting from firing are decisive for the performance of the final product:
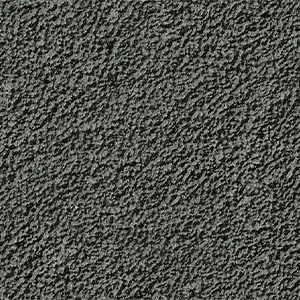
- flexural strength (up to 40–50 MPa for porcelain stoneware)
- controlled thermal expansion coefficient (essential for heated flooring)
- durability over time even under mechanical or thermal stress
Anti-slip properties, when required, are also influenced by the final microstructure obtained after firing, which can be designed by adding grit, reliefs or surface treatments, as in the NEXT EXPERIENCE SURFACES line by Sicer.
Irreversibility of the process
Once completed, firing is irreversible. There is no physical or chemical treatment that can restore the material to its original condition. This marks the complete transition from natural material to engineered material, with properties that depend as much on the initial composition as on the thermal curve applied.
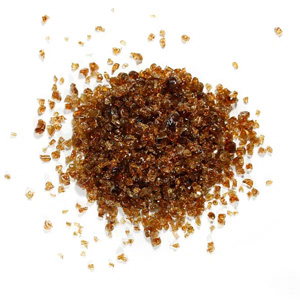
Glazes and vitrifying materials: the artificial contribution
Although ceramics originate from natural raw materials, a significant part of their aesthetic and functional properties depend on elements entirely developed in industry, such as glazes, vitrifying frits, and decorative materials. These components not only complete the production cycle but also radically modify its performance.
Composition and function of ceramic glazes
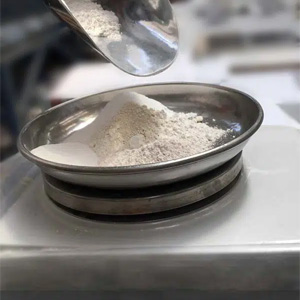
Ceramic glaze is a glassy mixture which, when applied to the surface of the ceramic substrate and then fired, forms a thin protective and decorative coating.
From a chemical point of view, glaze is composed of:
- glass-forming oxides (Na₂O, K₂O, CaO)
- glass-forming oxides (SiO₂, B₂O₃)
- stabilizers and modifiers (Al₂O₃, ZnO, TiO₂)
- pigments and opacifying agents
These components are premixed and subjected to high-temperature melting (1300–1500 °C), then rapidly cooled and ground: this is how ceramic frit is produced, the basis of almost all industrial glazes. This process is completely artificial: none of the stages occur in nature.
Functional and special glazes
In recent decades, there has been a shift from “neutral” glazes to advanced formulations capable of imparting high technical properties and aesthetic performance to ceramic surfaces. Glazes no longer play a passive protective role but have become an integral part of the functional design of the product.
Among the main features are:
- improved chemical and mechanical resistance, useful in industrial, contract, or outdoor environments;
- optimized interaction with digital inks, to ensure color stability during firing;
- aesthetic versatility, thanks to different surface finishes (glossy, matte, satin) and different melting curves.
Sicer offers a complete range of ceramic glazes for traditional or digital applications, formulated to guarantee:
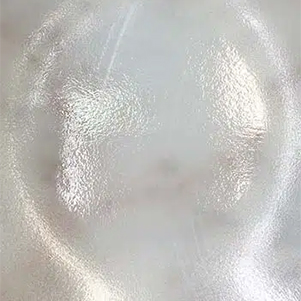
- controlled fusibility and compatibility with substrates,
- visual depth and transparency when required,
- targeted interaction with grits in relief applications using digital glue.
Sicer glazes are designed to adapt to the specific needs of each production cycle and integrate perfectly with contemporary decoration technologies, including multi-level digital applications and synergistic use with grits and adhesives.
Digital inks and advanced decorations
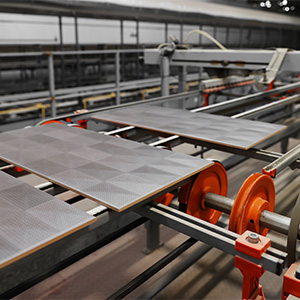
Ceramic decoration has undergone a radical transformation with the introduction of digital inkjet printing, which has replaced traditional screen printing and rotogravure methods. Digital ceramic inks are composed of suspensions of micronized oxides and pigments in organic vehicles or specific solvents, designed to ensure printing stability, fusibility, and interaction with glazes.
Today, the industry is evolving towards a new generation of high value-added inks that are not only capable of decorating but also of reducing the environmental impact of the production cycle.
Sicer is at the forefront with two advanced research lines:
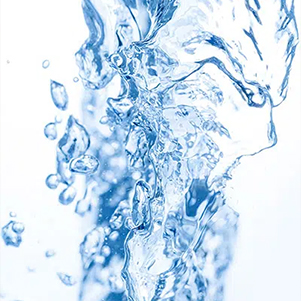
- LOW EMISSION (LE) eco-solvent-based inks, patented, with:
- certified reduction of VOCs, aldehydes, and TOCs by up to 70% compared to the best eco-inks on the market,
- no odor and high compatibility with all print heads,
- excellent aesthetic and color rendering,
- completely customizable base in terms of color and effect.
- WATER-BASED (WB) inks currently in an advanced stage of development, designed to combine graphic performance with maximum environmental compatibility and to prepare the sector for future regulatory developments in line with ESG.
These are complemented by water-based digital glue, designed for relief applications using grits: available in versions for high and low temperatures, it guarantees graphic precision, excellent adhesion, and minimal emissions.
Thanks to these investments, Sicer confirms its role as a technology partner for sustainable, certified, and high-performance ceramic decoration, contributing in a concrete way to the ESG objectives of ceramic manufacturers.
The role of decorative materials in final performance
In addition to their aesthetic value, decorative materials influence:
- abrasion resistance (e.g., hard grits vs. soft glazes)
- coefficient of friction (through texture and structured applications)
- UV resistance (light-stable inorganic inks)
- post-firing color results, which depend on interaction with the thermal curve
In summary, glazes, frits, and inks are the technological heart of ceramic tiles. They are the result of industrial research and represent its most obvious artificial contribution: an irreplaceable component, without which modern ceramic material would lose its most distinctive characteristics. And Sicer knows this well.
Technical classification: natural, artificial or hybrid?
The debate on the classification of ceramics as natural or artificial materials is not merely semantic, but has significant implications for laboratory technicians, R&D managers and buyers in the ceramics industry. A correct definition helps to position the product within industrial supply chains, compare it with alternative materials, and guide design choices in terms of sustainability, performance, and regulations.
Where do ceramics fit in?
When analyzing their composition, production processes, and final behavior, ceramics cannot be considered either fully natural or completely artificial, but clearly belong to the category of processed materials.
Technical criteria | Ceramic |
Origin of raw materials | Natural (clay, feldspar, quartz) |
Industrial processing | Extensive and irreversible |
Final composition | Different from the original |
Microcrystalline structure | Largely engineered |
Functionalization | Aesthetic, technical, mechanical |
During the production cycle, ceramic raw materials undergo changes that make them impossible to separate or return to their original forms. The final product is a composite, glassy, crystalline material that is inert, non-deformable, and high-performance.
Comparison with other building materials
To better understand the positioning of ceramics, it may be useful to compare them with other materials widely used in the construction and architectural sectors:
Material | Origin | Process | Technical classification |
Wood | Natural | Minimum | Natural |
Concrete | Natural + Artificial | High | Artificial (reactive) |
Glass | Natural | High | Transformed (amorphous) |
Plastic | Synthetic | Very High | Artificial |
Ceramic | Natural | High | Transformed material (hybrid) |
This hybrid positioning gives ceramics versatility of application, but also requires greater awareness in production cycle management, technical communication, and design choices.
Implications for the ceramic sector
Classifying ceramics as a high-tech processed material has concrete implications on various fronts:
- In technical communication with designers, architects, and buyers
- In environmental assessment and LCA
- In the search for decorative and functional solutions that fully exploit the possibilities offered by its engineered nature
Understanding and correctly communicating the hybrid nature of ceramics is not just an academic issue, but a tool for generating value throughout the supply chain, from formulation to technical marketing.
Environmental aspects and sustainability
Any reflection on the nature of ceramics must include an assessment of its environmental impact. In an industrial context that is increasingly focused on circularity, decarbonization, and ESG standards, understanding the sustainability of ceramic materials is essential for R&D managers, buyers, and strategic decision-makers.
Environmental impact of raw materials
The raw materials used in ceramic production—clays, feldspars, quartz—are derived from non-renewable extraction processes. However:
- they are abundant in nature,
- they do not require complex chemical processes to be used,
- they do not release hazardous substances during use or at the end of their life cycle.
The real environmental issue is not their natural origin, but the way in which these resources are extracted, transported, and managed. Using local suppliers or those with a low logistical impact significantly reduces the carbon footprint.
Energy-intensive production processes
The main critical issue in the ceramic sector is its high energy requirement:
- drying and firing require large amounts of heat (often from fossil fuels),
- continuous firing involves direct emissions of CO₂, nitrogen oxides (NOₓ), sulfur (SOₓ) and particulate matter.
It is at this stage that companies can implement sustainability strategies:
- optimization of thermal cycles,
- heat recovery from kilns,
- use of alternative fuels or methane/hydrogen mixtures,
- digitization of process control to reduce waste and scrap.
Comparison with artificial materials
Compared to totally artificial materials (such as resins, PVC, linoleum), ceramics:
- do not emit VOCs (volatile organic compounds),
- do not degrade under the action of heat or UV rays,
- do not release microplastics,
- have an average lifespan of over 30 years in building applications.
This intrinsic longevity partly offsets the high impact of the production phase, making ceramics a preferable choice from an LCA (Life Cycle Assessment) perspective.
Recyclability and end-of-life management
Fired ceramic material is chemically inert, non-biodegradable, but recyclable in numerous secondary applications. Among the main uses are:
- crushing for road sub-bases, draining screeds and inert fillers;
- inclusion in secondary ceramic mixtures for rustic or technical products with low plasticity;
- use in pozzolanic cements, as a partial replacement for high-emission clinker;
- application in sound-absorbing or industrial insulation products.
At the same time, many ceramic companies have implemented internal circular economy practices, including:
- recovery of raw waste (mixtures, grit, unfired glazes),
- reintegration of glaze or ink residues into subsequent cycles,
- reuse of process water through recirculation and treatment plants.
Sicer is also actively engaged on this front: process water reuse systems are implemented in its production plants, reducing overall water consumption and improving the environmental efficiency of the entire decorative cycle. This approach, part of a broader vision of certified sustainability, contributes to the ESG objectives of the supply chain and the transition to more responsible industrial ceramics.
The Sicer case: innovation and integrated sustainability
Sicer has invested strategically in the search for digital decorative solutions with low environmental impact, with a particular focus on reducing VOC emissions and complying with ESG criteria.
The main innovations include:
- LOW EMISSION digital inks, solvent-based with a patented formula, which significantly reduce emissions of Volatile Organic Compounds (VOCs), aldehydes and TOCs, improving environmental conditions in production;
- WATER-BASED digital inks, currently in an advanced stage of development, designed to combine sustainability and graphic performance with a view to the future;
- water-based digital adhesives, used for relief applications with grits, which guarantee adhesion, aesthetic precision, and low emissions.
These solutions not only improve the environmental impact of the decorative cycle, but are also a key element in the ESG strategy of many ceramic manufacturers. In a market that is increasingly attentive to traceability, chemical safety, and transparency, Sicer is a technological partner for the sustainable transition of the ceramic industry.
Contemporary innovations in the sector
The evolution of the ceramic sector over the last twenty years has accelerated considerably, driven by three main factors: process digitalization, surface functionalization, and environmental sustainability. For R&D managers and laboratory technicians, keeping track of these changes means anticipating market trends and focusing product development on increasingly complex performance and regulatory requirements.
Advanced decorative materials
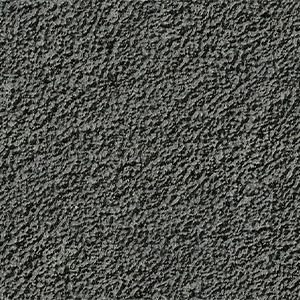
Decorative materials are no longer simple aesthetic tools, but true functional agents capable of influencing the performance of ceramic surfaces.
Today, thanks to complex formulations and multi-layer applications, decorations can integrate:
- advanced optical effects (metallic, pearlescent, opalescent),
- differentiated mechanical resistance (hard grits for high-traffic areas),
- specific functions such as antibacterial or photocatalysis (e.g., UV-activated titanium dioxide).
The calibrated micro-grains offered by Sicer in the NEXT EXPERIENCE SURFACES line are a clear example of how decoration can also affect the coefficient of friction, improving slip resistance while maintaining high cleanability and aesthetic quality of the surface.
Digital technologies and inkjet printing
The transition from screen printing to digital inkjet decoration has transformed the relationship between design and ceramic production:
- work is carried out on color databases and digital textures,
- decoration is integrated with 3D surface modeling (textured effects, reliefs, engravings),
- raw material consumption is reduced, and yield per square meter is optimized.
This context has given rise to innovations such as:
- digital glue: allows selective applications of grits to create precise and repeatable three-dimensional effects;
- water-based inks: reduce VOC emissions and improve environmental safety;
- predictive software for managing firing curves and color optimization in the kiln.
Eco-friendly formulations
New regulatory and market demands are driving a move towards cleaner and more transparent chemistry. Innovations in this area include:
- low-emission frits, designed to melt at lower temperatures and release less greenhouse gases;
- lead- and cadmium-free glazes, compliant with REACH regulations;
- closed production flows, which recycle water, raw waste, and glazing residues.
In line with this direction, Sicer has developed a complete range of decorative products focused on process sustainability, combining chemical research with production efficiency and environmental compatibility.
Trends: from standardization to customization
An emerging trend is the shift from standardized mass production to on-demand customization:
- micro-batches on demand,
- on-demand decorations for architects and contract work,
- functionalized surfaces for niche applications (e.g., healthcare, horeca, industrial technical coatings).
This flexibility is made possible by the combination of smart materials and digital technologies, which enable the creation of high value-added products even in small volumes.
Sicer technical grits: the engineered contribution to ceramic surfaces
The high-strength transparent grits (GHR line) and polished grits for dry applications (GRA DRY-LUX line) represent one of the most technologically advanced solutions developed by Sicer for the functionalization of ceramic surfaces. They are the result of a careful selection of glass raw materials and advanced melting and granulation control.
Distinctive features include:
- high optical transparency, which enhances digital graphics;
- resistance to abrasion and chemical agents;
- customizable friction coefficient, useful in high-traffic environments;
- can be applied wet or dry, with a wide choice of grain sizes.
From a technical point of view, the Sicer range stands out for:
- the presence of functional crystalline phases (wollastonite, plagioclase) as highlighted by XRD analysis;
- continuous control of composition and fusibility;
- optimization of tension and flatness through preliminary study with a flexometer.
The grits thus become an active technical element in defining the surface performance of the ceramic material, further reinforcing the article’s thesis: contemporary ceramics are an engineered system in which aesthetics, function, and technology coexist synergistically.
Discover the complete range of Sicer technical grits
Scientific conclusions on the nature of ceramics
Technical analysis shows that ceramics cannot be classified as either a purely natural or completely artificial material. It is a transformed material, whose hybrid nature arises from a complex combination of:
- raw materials of geological origin,
- highly technological industrial processes,
- advanced functionalizing interventions (glazes, inks, grits),
- irreversible chemical-physical transformations during firing.
This composite nature is what makes ceramics such a versatile and highly valued material in architectural, technical, and decorative contexts.
A new possible definition: naturally based engineered material
We can define modern ceramics as a naturally based engineered material, where the origin of the raw materials remains recognizable, but the behavior of the finished product is completely new, designed to meet:
- mechanical requirements,
- aesthetic needs,
- regulatory and environmental constraints.
In other words, ceramics is both design and material, the tangible result of a process that combines materials science, color engineering, sustainability, and industrial culture.
Implications for the ceramic sector
For the ceramic sector, this awareness represents a strategic lever:
- it allows industrial know-how to be valued as a distinctive feature,
- it guides R&D choices towards increasingly high-performance and sustainable formulations,
- it strengthens the competitive position of manufacturers who invest in innovation.
Knowing how to communicate the scientific and technical complexity of ceramics correctly, without reducing it to simplistic slogans, also becomes a critical factor in relations with architects, general contractors, buyers, and stakeholders who are sensitive to sustainability.
Conclusion
The initial question – ceramic: natural or artificial material? – can only be answered by recognizing its hybrid, engineered, evolutionary nature. It is this complex identity that constitutes the true strength of contemporary ceramic material: a sophisticated balance between natural roots and an industrial future.
FAQ
FAQ
Ceramic is a transformed material : it derives from natural raw materials, such as clays and feldspars, but is radically modified through industrial processes—crushing, shaping, firing—that alter its structure, composition, and behavior. The result is an engineered, stable, and functional material.
Technically, neither . Ceramic falls between natural and artificial materials, as it is produced from natural components but undergoes physical and chemical transformations that make it a new product compared to the geological origin of its raw materials. The definition of hybrid or transformed material is correct.
– Natural: materials available in nature and used with minimal modification (e.g., wood, stone, raw clay).
– Artificial: materials synthesized entirely in a laboratory or industrial plant (e.g., plastic polymers, fiberglass, epoxy resins).
– Transformed (such as ceramics): natural materials subjected to extensive processing that modifies their original structure.
Ceramic raw materials come from natural geological deposits:
– le clays derive from sedimentary rocks rich in aluminum silicates,
– i feldspars are intrusive minerals from magmatic rocks,
– il quartz is a common constituent of many siliceous sands.
These materials are selected, refined, and industrially processed to create tiles, coatings, and technical ceramics.