Ceramic pigments are special solids, reduced to particles that can be colorful, black or white. These elements are widely used to color tiles, tableware, sanitary ware, glazes and glass and they are mainly used by producers of raw materials and semi-finished products for the ceramic industry.
The ceramic pigment, basically, gives the color and does it through the simple physical dispersion in what it has to color, without being dissolved in the liquid phase that is formed at high temperature during firing.
Among the most important pigments are: praseodymium yellow, cobalt blue, iron, selenium and calcium-tin-chromium pink, iron and manganese brown, chromium-iron-cobalt black.
The production of some ceramic pigments and the declination into pigments for ceramic inks is one of the several activities of Sicer, a UNI EN ISO 9001: 2015 certified company for the design and manufacture of raw materials, glazes, digital inks and dyes for the ceramic industry.
In particular Sicer uses ceramic pigments for the production of different products.
The .E SERIES fatty acid ester-based inks and the .LE series of solvent-based inks are obtained by ultra-grinding of ceramic pigments of own production, in organic and super-dispersing vehicles designed to confer stability over time. The solvents used for these inks guarantee excellent performance and minimal odor emissions, which become non-existent in the case of .LE LOW EMISSION inks.
Also Sicer range of SK Colored Oxides includes brilliant pigments suitable both for the glazes and the ink production.
TECHNICAL-PHYSICAL CHARACTERISTICS OF CERAMIC PIGMENTS: WHAT MAKES THEM UNIQUE AND EFFECTIVE
Pigments are used in several industrial applications, in the ceramic sector and in the stains for ceramic tiles, but for a good quality and to be really effective these elements have to show some specific characteristics.
In particular:
- High coloring power: the color has to be intense and have a high refractive index to ensure shine;
- Chemical stability: it has to maintain its characteristics during the firing of the ceramic body, that is, it has not react with the other components by melting and/or forming a new phase;
- Thermal stability or refractory properties: optical properties has not to change even at very high firing temperatures. Often the thermal stability is much lower than the theoretical one, therefore the melting point of the pigments has to be considerably higher than the ceramic firing temperature. The pigments should have a melting temperature between 1600-2000 C.
In addition to these technical-physical characteristics, ceramic pigments have to show other “qualities” that can meet the needs of the industrial production.
It is required:
- Low toxicity: they have to comply with the limits permitted by international standards regarding toxic elements, meeting certain health requirements. This ensures the protection of both operators and the environment.
- Cost of raw materials cin line with the market: the raw materials, from whose reaction the final structure will be generated, has not be difficult to find or excessively expensive.
HOW DO CERAMIC PIGMENTS ORIGINATE? THE PRODUCTION PROCESS
Many pigments, despite the complex production process, are considered by the market as raw materials.
However, the industrial ceramic pigments are the result of the reaction to the solid state to the high temperature (1000-1400 C) of oxides and other raw materials.
Here follows a summary of the production process of ceramic pigments.
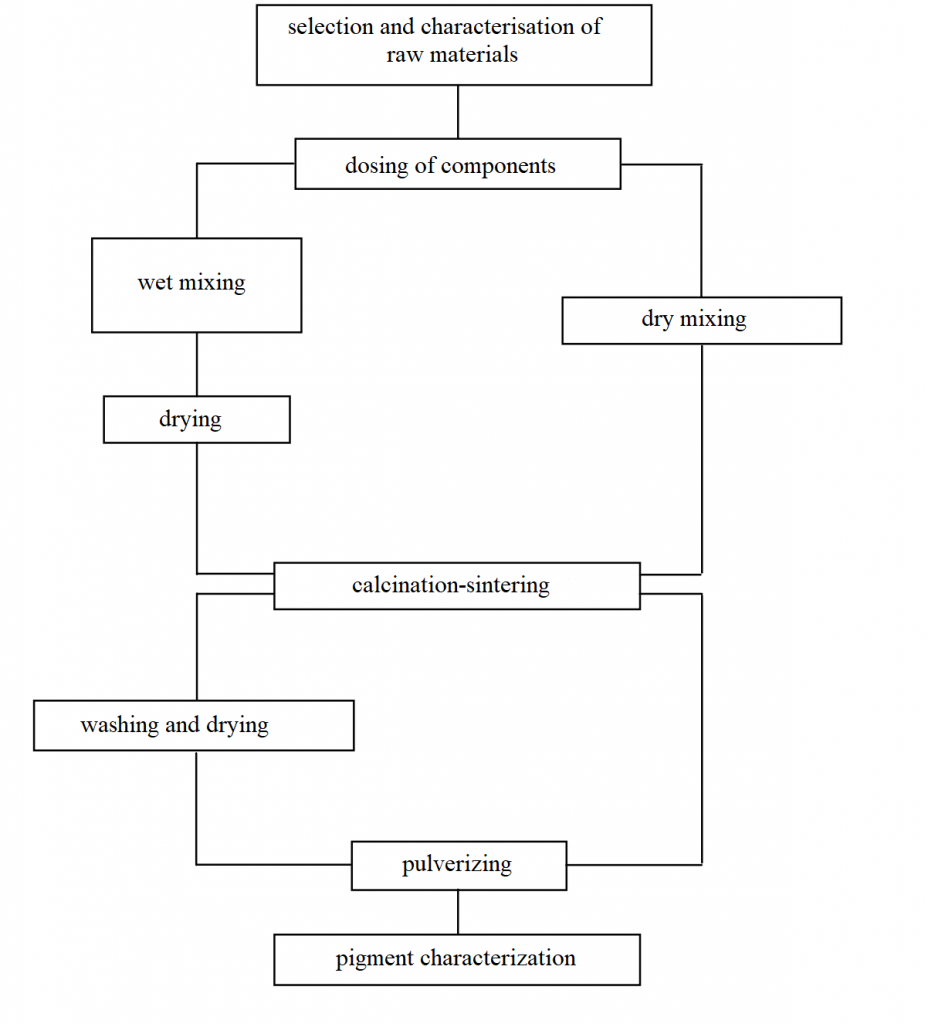
During the selection of raw materials, significant parameters have to be checked: purity, specific surface area and grain size distribution of the raw materials, as the reactivity of the mixture depends on these characteristics.
- The dosage requires special care to avoid significant variations in the final product.
- Mixing is essential to obtain an intimate mixture among the oxides of reagents during calcination.
- Calcination is the phase in which the reactions to the solid, liquid and gaseous state of the various components occur, with the formation of the desired crystalline compound.
- The grinding completes the production process by substantially influencing the coloring power, the tonality and the chemical resistance of the pigment.
Finally, after the grinding, the pigment is subjected to washing treatments with water to eliminate the toxic or unwanted phases that may vary the pigment-paste or pigment-glaze interaction.
HOW TO CLASSIFY A CERAMIC PIGMENT
The classification of ceramic pigments can be done according to different criteria. They can be divided for the origin, the given color, the crystalline structure of the pigment and its final use.
Classification for origin
A ceramic pigment can be natural or synthetic.
The first one can be sought in the nature. They have long been known and used by people. The limit of this type of pigments is the high amount of impurities they contain.
Synthetic pigments, unlike natural ones, are industrially prepared by appropriate chemical processes and represent the vast majority of pigments. They are the result of synthesis coming from oxides or carbonates and because of the different preparation stages needed to get the finished product, they are more expensive.
Color classification
Through mixing or using individual pigments, the main colors can be obtained. In addition, several crystal structures can give different colors.
Here is an example of the colors that can be obtained with ceramic pigments.
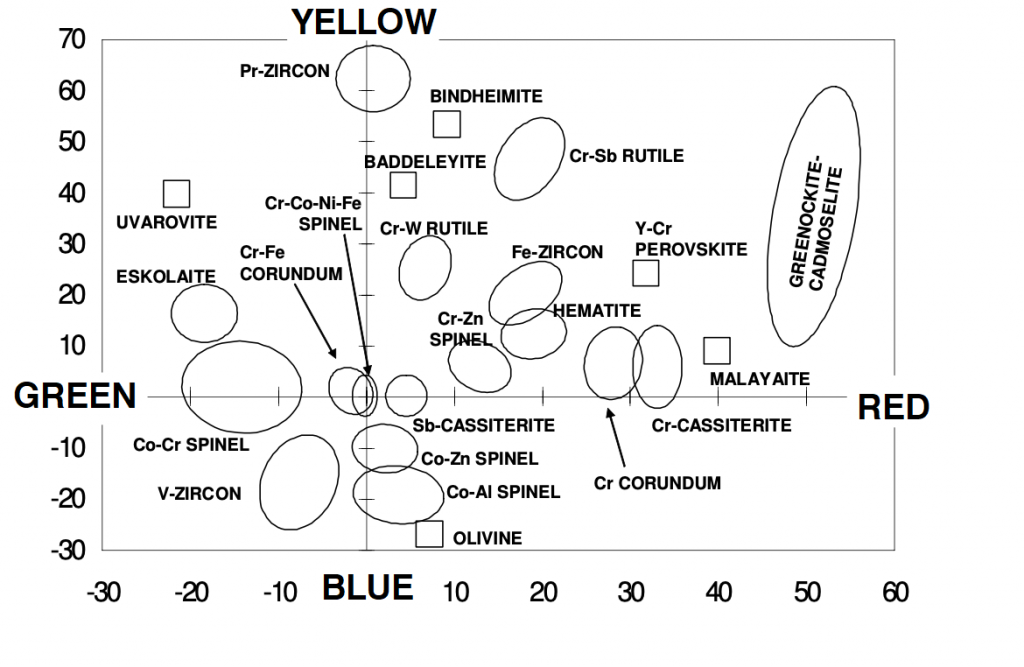
Sicer, a state-of-the-art company, has been able to use pigments in order to create inks with unique colors. The exclusive Ink Brillant Yelllow and Ink Vibrant Red guarantee excellent results with ultra brilliant colors and excellent visual quality.
In particular, the absolute Red and Yellow colors can create exclusive and original collections, with more and more natural details and a better visual quality and real colors.
The whole range of digital inks (SINK) (link) is approved for the most modern digital machines for the production of large and non-large slabs.
These innovations have been possible thanks to the constant research of the Technology Sicer Lab, which by associating high skilled tools with highly qualified technical staff can obtain product results of the highest level.
Classification for crystalline structures
As regards the classification based on crystalline structures, four main types of minerals can be distinguished, which can be used as pigments:
- Idiochromatic compounds that contain chromophore ions as main constituents of the crystalline structure;
- Allochromatic compounds in which coloring is given by the presence in small quantities of a transition metal or rare earth;
- Heterogeneous or heteromorphic compounds, these are non thermally stable pigments that are included within a colourless and transparent crystalline structure that increases their thermal stability;
- Mordant pigments or chemical-adsorbed pigments, these are pigments in which the dye phase, colloidal in size, is adsorbed on the surface of the host phase by binding forces.
To offer you an even more detailed classification of colored inorganic pigments, we attach here below the classification of the CPMA, Pigments Manufacturers Association, Inc., the only US trade association representing manufacturers of colored pigments, intermediate suppliers, distribution companies and service providers in North America.
CPMA – Classification And Chemical Descriptions Of The Complex Inorganic Color Pigments
Classification for final use
On the basis of their final use, ceramic pigments can be divided into three main groups: pigments for body stain, ceramic pigments for glazes and pigments for INKS.
The pigments for body stain are mixed with the ceramic paste. The colour given depends on the natural colour of the paste, the atmosphere of the industrial furnaces and the firing cycle.
The pigments for glazes are mixed with the glass-crystalline coating of a ceramic body and give color by dispersion within these materials.
Finally, the pigments for INKS represent the most complex category because they depend on the several technological changes and evolutions caused by the advent of digital technology.
Specifically, the color and its development on ceramic surfaces have faced some important changes:
- from glass (glaze or mass-colored screen printing) to digitized pigment protected by a glass layer (glossy or matt)
- from ground pigment up to 5-10 microns in diameter to 0.5-1 micron pigment (with the consequent loss of colors: the more I grind a dye the more I lose the colors)
- from droplet volume (dots) of microliters to dots of picolitres, due to the resolution of the “drop on demand” system.
Furthermore, the sensitivity to the “boundary” conditions given by bio glaze / firing glaze has drastically increased, increasing the demand for highly performing pigments.
All these changes and evolutions in the processing and use conditions have made the ceramic pigment today:
- more intense
- more stable
- easier to grind
However, the search for all these characteristics had to take into consideration the increasingly significant environmental requirement in recent years; in fact, it is essential not to generate polluting or non-reusable production residues.
Another element that continues to influence the research and production of pigments for inks is the continuous request to increase the printing surface on ceramic tile, to reach the levels of printing on paper or plastic.
So, we moved from normal and penalizing four-color process to real quadricromia with true red and yellow tones, up to hexachromies or even optacromies.
THE MARKET FOR CERAMIC PIGMENTS
Many Italian companies and producers of raw materials and semi-finished products for the ceramic industry prefer to import the raw materials or even the ceramic pigments.
This is because domestic production is very expensive at energy level.
To maintain competitiveness and lower consumption, it is necessary to rationalise the process and search for alternative raw materials.
Some innovations to the production process have been applied to the synthesis and blending phase to lower energy consumption, but this often means having to modify also the plants.
Furthermore, the disposal of production waste requires a very complex process with specific requirements to be respected.
One of the questions we ask ourselves today is therefore, whether Italian companies should continue to import from other countries with additional costs and charges or should invest to convert the plants and start an internal production of ceramic pigments.
In light of what is happening today, due to the health emergency caused by the COVID-19 this choice could become an opportunity.
Modifying and improving the internal production processes should be considered not a cost, but an investment.
These optimizations would first of all face the Italian demand for materials and pigments that could, for reasons of force majeure as in this period, not always be satisfied.
Secondly, the increased availability of pigments would help the producers of raw materials and semi-finished products for the ceramic industry to expand and improve the range of products offered.
Finally, the possibility of intervening directly on an internal production process by improving it at a technological and scientific level can give an added value to its finished products compared to those of competition.
This philosophy of continuous research, development and innovation are in fact the cornerstones of Sicer that through its R&D Lab and technology Lab, features high technical level of the products and attention to innovation and aesthetic research, always respecting the environment.
Discover the products
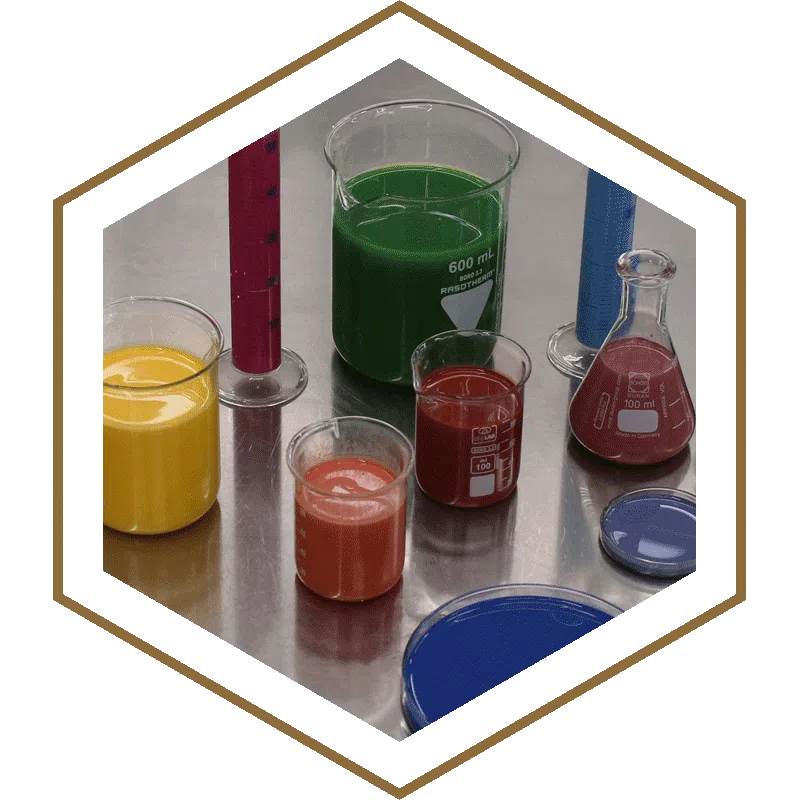