Index
- Introduction
- General principles of ceramic strength
- Mechanical strength: standard tests and influencing factors
- Wear and abrasion resistance: PEI classification
- Thermal resistance and thermal shock: behaviour under thermal cycles
- Chemical resistance: tests and exposure conditions
- The role of vitrifying materials in resistance
- Quality control and parameter optimisation
- Technological innovations to improve resistance
- Industrial applications and choice of materials
- Conclusion
- FAQ
Introduction
The main types of resistance relevant in the industrial sector include:
- Mechanical resistance, i.e. the ability to withstand bending, compression and impact without fracturing. Essential for floors and surfaces subject to loads.
- Abrasion and wear resistance, particularly important in high-traffic commercial and industrial environments, where durability over time is required.
- Thermal and thermal shock resistance, essential for surfaces exposed to hot-cold cycles or high temperatures, such as outdoors or in production environments.
- Chemical resistance, necessary in environments subject to contact with acids, bases, detergents and solvents, such as in the food, healthcare or chemical industries.
These aspects determine the functionality and durability of ceramic materials and guide the choice of the most suitable products according to the conditions of use.
General principles of ceramic resistance
The strength of a ceramic material is largely determined by its internal structure and the chemical and physical interactions between its components. The following characteristics are key to understanding its behaviour in industrial applications:
Crystal structure and atomic bonds
Ceramic materials consist of a combination of crystalline and vitreous phases. Crystalline phases have regular crystal structures, in which atoms are bonded together by ionic or covalent bonds, both characterised by high bond energy. This configuration confers rigidity and stability but limits plastic deformability, making ceramics more susceptible to fracture when subjected to high and concentrated stresses.
Fundamental mechanisms of resistance
At the molecular level, resistance depends on the continuity of the crystal lattice and the absence of structural defects that could act as fracture initiation points. The mechanisms of cohesion between grains, the adhesion between phases and the homogeneous distribution of particles contribute significantly to mechanical and thermal performance.
Influence of porosity and microstructure
Excessive or poorly distributed residual porosity reduces the strength of the material. In industrial ceramic processes, the presence of open or closed pores is minimised by adjusting the firing parameters, grain size and pressing. The microstructure resulting from an optimised process has uniform grains and well-integrated phases, promoting mechanical strength and abrasion resistance.
Theory of microfracture propagation
Ceramics, being fragile materials, are subject to brittle breakage, i.e. without prior plastic deformation. Microfractures are triggered by structural defects and propagate rapidly under critical loads. Standard tests (e.g. ISO 10545-4) assess flexural strength precisely in relation to this vulnerability. The quality of sintering and the homogeneity of the ceramic mass are fundamental elements in limiting the propagation of fractures.
Mechanical resistance: bending, compression, impact
Mechanical strength is a fundamental parameter for assessing the suitability of ceramic materials in applications subject to static and dynamic loads. International standards, such as ISO 10545-4, define methods for measuring flexural and compressive strength in the laboratory.
Bending strength analysis
Flexural strength (also known as breaking modulus) measures the ability of a material to resist a force distributed over a surface. It is assessed by applying a load to a tile supported at two points until it breaks. The resulting values vary depending on:
- size and thickness of the sample
- regularity and densification of the microstructure
- presence of internal microcracks
Greater uniformity of the ceramic body and well-controlled firing contribute to increased flexural strength.
Compressive strength: mechanisms and values
Ceramic materials tolerate compressive loads very well thanks to the rigid nature of their crystal lattice. Compressive strength is measured by applying increasing vertical loads to test specimens of controlled dimensions. Here too, the value depends on the density of the material and the absence of porosity or inclusions. This test is less common than the flexural test, but is important in structural applications or for vertical applications (e.g. load-bearing cladding).
Impact resistance and toughness of ceramic materials
Impact resistance is lower in ceramic materials than in other structural materials due to their low toughness. Toughness describes the ability to absorb energy without fracturing. To verify this, tests such as mass drop on ceramic specimens or instruments dedicated to measuring fracture propagation are used. In general, ceramics with a homogeneous structure and consistent thicknesses are more resistant to small, localised impacts.
Reference standard tests
The main standard tests for evaluating mechanical properties include:
- ISO 10545-4: Determination of flexural strength and fracture toughness
- ASTM C1161: Method for flexing rectangular ceramic specimens (mainly applied to technical ceramics)
These tests are standardised to ensure the comparability of results between different materials, manufacturers and test conditions. Test documentation is often required in the technical data sheets of products intended for high-stress environments.
Resistance to wear and abrasion
Wear resistance is one of the most important properties of ceramic materials intended for use in flooring and high-traffic surfaces. Wear can be caused by mechanical friction, rubbing, the presence of abrasive debris or the movement of loads. The behaviour of the material in these contexts is decisive for its durability over time.
Surface wear mechanisms in ceramic materials
In ceramic materials, wear occurs through the gradual removal of the glaze or the outer surface of the substrate. Constant mechanical action from shoes, wheels, sand and other abrasive agents can cause micro-grooves, loss of shine or, in the most serious cases, material removal and colour alteration.
Usury can be divided into:
- surface abrasion (gloss, finish)
- deep abrasion (structure, colour, enamel)
Factors affecting abrasion resistance
Several factors contribute to determining the degree of resistance of a ceramic material to wear:
- Type of glaze or finish: High-hardness vitrified glazes guarantee greater resistance.
- Density and porosity of the substrate: A porous substrate tends to yield more quickly under abrasive stress.
- Thickness of the surface layer: The greater the useful thickness, the more resistant the material is to erosion.
- Grain size of abrasive agents: Fine sands can be more insidious than coarser ones.
PEI classification and test methods for wear
The standard method for determining wear resistance is ISO 10545-7, which defines the PEI (Porcelain Enamel Institute) classification. This method involves exposing the ceramic sample to standardised abrasion cycles with specific abrasive agents.
The PEI scale is structured as follows:
PEI class | Recommended use |
PEI 1 | Bathrooms and bedrooms (light traffic) |
PEI 2 | Residential areas excluding kitchens and hallways |
PEI 3 | Residential areas for moderate use |
PEI 4 | Residential and commercial environments with medium traffic |
PEI 5 | Intense public, industrial and commercial environments |
The test measures the variation in surface appearance and loss of material as a function of cycles.
Role of enamels and surface treatments in wear resistance
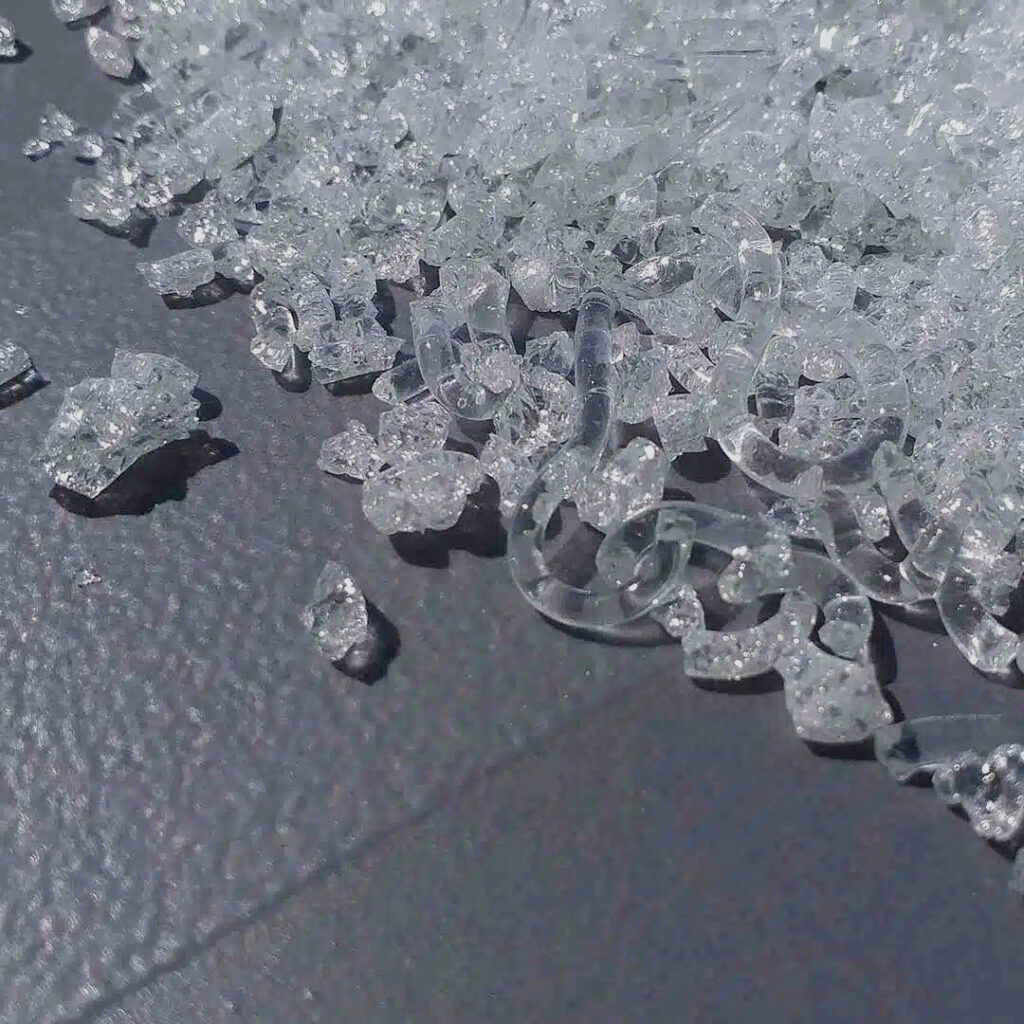
The choice of glaze and vitrifying materials directly affects the abrasion resistance of ceramic surfaces. Glazes with a vitrified composition and high hardness help improve surface resistance. Depending on the application requirements, different surface technologies based on technical grits can be used.
Sicer offers a wide range of high-resistance grits designed to improve surface performance. These include:
- The NEXT EXPERIENCE SURFACES line, made with micro-grains of calibrated size, allows for opaque, anti-reflective, chemical-resistant and easy-to-clean surfaces.
- the GHR – High Resistance Grits series, designed for floors subject to intense stress, allows for the creation of naturally textured, non-slip, abrasion-resistant surfaces with excellent graphic performance even in dark shades;
- the GRA – Dry Lux line, specifically for dry application and mirror lapping, allows for the creation of extremely bright and compact surfaces with high chemical resistance, cleanability and flatness, thanks to an optimised selection of frit and calibrated grain size.
All these solutions integrate Sicer’s expertise in the design of surface materials that combine aesthetics and technical performance, adapting to different production cycles and intended uses.
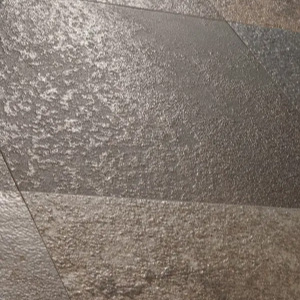
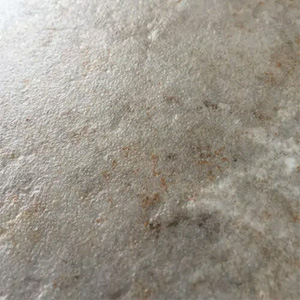
Thermal resistance and thermal shock
Due to their inorganic and non-metallic nature, ceramic materials have good thermal stability, making them suitable for applications in environments subject to significant temperature variations. However, their behaviour under thermal stress depends on various microstructural factors and must be assessed through specific tests.
Behaviour of ceramic materials under temperature variations
Ceramics respond to thermal variations with volumetric expansion and contraction, which can generate internal stresses, especially in the presence of heterogeneous phases or structural discontinuities. If the stresses exceed the elasticity threshold of the material, microcracks or delamination between the glaze and the substrate may occur.
Thermal expansion coefficient and its implications
The linear thermal expansion coefficient (α) measures the dimensional variation of the material as a function of temperature. Poor compatibility between the coefficient of the substrate and that of the glaze can generate differential stresses during firing or in the stages of use, compromising the mechanical strength and aesthetic integrity of the product.
The optimisation of ceramic compositions therefore requires a balanced choice of raw materials and vitrification agents to reduce the differences between the phases involved.
Resistance to frost and thermal cycles
Frost resistance is a fundamental requirement for ceramic materials intended for outdoor use. The tests required by UNI and ISO standards (such as ISO 10545-12) involve freezing and thawing cycles in the presence of water to simulate real exposure conditions. Any residual porosity, if open and capillary, can absorb water and cause internal breakage due to expansion during freezing.
The quality of the pressing and the absence of microcavities are essential to ensure good frost resistance.
Thermal shock: causes, mechanisms and prevention
Thermal shock is caused by rapid and significant changes in temperature (e.g. from +150°C to room temperature), which can cause sudden fractures in materials with low thermal conductivity or high rigidity.
The ISO 10545-9 standard defines the test criteria for thermal shock in glazed tiles, subjecting samples to alternating immersion in cold and hot water. A product is considered compliant if, at the end of the cycle, it shows no obvious signs of deterioration (cracks, detachment, variation in gloss or colour).
The optimal design of the firing cycle, the use of raw materials with high thermal stability and the absence of residual porosity are key factors in preventing damage from thermal shock.
Chemical and aggressive agent resistance
Chemical resistance is a fundamental property for ceramic materials intended for industrial environments, healthcare facilities, laboratories, professional kitchens or outdoor areas exposed to contaminants. It indicates the ability of the ceramic surface to maintain its characteristics when in contact with potentially corrosive or altering chemical agents.
Chemical attack mechanisms on ceramic materials
Chemical attack can occur through selective solubilisation of the glass components, colour alteration, opacification, stain formation or surface changes. The most susceptible materials are those with an unstable glass phase or accessible residual porosity, which facilitates the penetration of reactive liquids.
The action can be:
- superficial, with loss of shine or colour variations
- structural, in severe cases, with weakening of the glazed surface
Resistance to acids, bases and organic solvents
Properly vitrified glazed ceramic surfaces generally have good resistance to:
- organic acids (e.g. citric acid, lactic acid)
- diluted inorganic acids (e.g. hydrochloric acid, sulphuric acid)
- alkaline bases (e.g. caustic soda, ammonia)
- organic solvents (e.g. alcohol, professional detergents)
However, performance depends on the composition of the enamel, the firing level and the finish. A porous or not completely sintered surface may be more susceptible to chemical attack.
Behaviour in the presence of salts and atmospheric agents
Exposure to de-icing salts (such as sodium chloride or calcium chloride), acid rain, humidity and atmospheric agents can alter the appearance and functionality of surfaces that are not adequately protected over time. In outdoor environments, it is therefore essential to use waterproof products with complete vitrification and minimal water absorption.
The installation conditions (joints, seals, slope) also affect the material’s ability to withstand severe environmental conditions over time.
Chemical resistance testing according to international standards
The performance of ceramic materials against chemical agents is regulated by international standards:
- ISO 10545-13: tests the resistance of glazed tiles to chemical attack by acids and bases, classified according to the type of visible or detectable alteration
- ISO 10545-14: assesses stain resistance, which is particularly important for surfaces used in healthcare, domestic or commercial environments
The samples are subjected to prolonged exposure to aggressive substances, and the result is classified according to the effect produced (no change, opacification, colour change, etc.).
The role of vitrifying materials in resistance
Ceramic glazes and vitrifying materials play a fundamental role in determining the surface performance of the finished product, directly affecting its mechanical, chemical and wear resistance.
How enamels and vitrifying materials influence resistance properties
The glaze is the outer layer of the ceramic material and can be formulated to offer:
- greater resistance to abrasion (thanks to the presence of hard, stable glass phases)
- protection against chemical agents and stains
- resistance to thermal shock and environmental changes
Furthermore, uniform application of the enamel and good thermal expansion compatibility with the substrate prevent detachment or micro-cracks over time.
Specific formulations to increase surface resistance
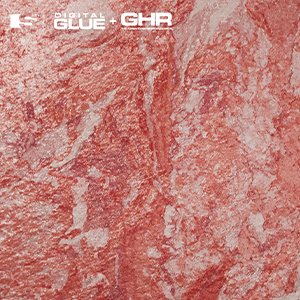
High-performance vitrifying materials are developed through carefully calibrated combinations of frits, grits, pigments and additives, with the aim of improving:
- the compactness of the surface layer
- the resistance to scratches and wear
- the resistance to chemical corrosion
Innovative technologies for improved performance
The evolution of ceramic technologies has led to the development of vitrifying materials:
- Ready to use, for quick and controlled application
- With integrated functional additives to increase resistance and adhesion
- Suitable for optimised firing cycles for surface stability
These solutions are designed to reduce aesthetic defects and ensure high performance even in demanding environments.
Balance between aesthetics and technical properties in enamels
One of the main challenges in designing ceramic glazes is achieving an effective balance between technical performance (wear resistance, ease of cleaning, thermal compatibility) and aesthetic quality (brightness, depth, uniformity). High-hardness glazes must still:
- maintain the desired gloss or matt finish
- guarantee excellent colour rendering, even on complex graphics
- ensure surface uniformity and stability on large formats
Sicer faces this challenge with continuous research into raw materials, pigments, frits and additives, developed to be perfectly integrated into the most advanced production cycles.
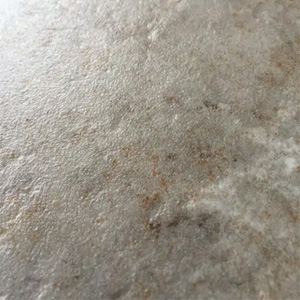
A concrete example is the GRA – Dry Lux series, designed for dry application with subsequent mirror lapping. These transparent and compact grits allow for highly brilliant surfaces with total glass-like transparency, scratch resistance, excellent cleanability and a controlled thermal expansion coefficient. Their minimally porous structure and optimised optical response enhance digital colours, ensuring excellent aesthetic results on all formats. Sicer thus confirms its position as a technological partner for ceramic companies seeking high-performance coating materials that meet increasingly sophisticated functional requirements and aesthetic expectations.
Quality control and strength optimisation
The performance of ceramic materials depends largely on the control of the process stages. An effective quality control system allows the consistency of mechanical, chemical and surface properties to be verified and any deviations that could compromise the final strength of the product to be corrected.
Methods for checking resistance properties in production
Ceramic companies adopt protocols for sampling and periodic testing on production batches, with tests carried out in accordance with international standards (e.g. ISO 10545). The properties monitored include:
- flexural strength (ISO 10545-4)
- abrasion resistance (ISO 10545-7)
- thermal shock (ISO 10545-9)
- chemical resistance and staining (ISO 10545-13, -14)
The results are compared with the expected technical specifications and can be recorded in statistical process control (SPC) systems to ensure traceability and efficiency.
Process parameters affecting final strength
The main variables that influence the mechanical and surface performance of the material include:
- temperature and baking curve
- time spent at peak
- degree of pressing and compaction of the dough
- residual moisture in the raw pieces
- grain size distribution
Even small variations in these parameters can alter the residual porosity, sintering and internal cohesion of the ceramic structure, negatively affecting strength.
Techniques for optimising firing cycles to maximise resistance
The firing cycle is one of the most critical elements in obtaining high-performance ceramic surfaces. Optimisation techniques include:
- fine adjustment of the heating and cooling curve
- stable maintenance of the peak temperature
- adaptation of the cycle to the type of enamel or vitrifying material used
The aim is to achieve uniform vitrification, avoiding internal stresses, bubbles, surface defects or unevenness that could weaken the product.
Correlation between chemical composition and final properties
The chemical composition of the mixture and glaze directly influences the strength of the material. The choice and dosage of:
- fluxes (borates, alkalis)
- refractory materials (silica, alumina)
- specific additives (opacifying agents, stabilisers)
must be studied according to the desired performance result. The balance between crystalline and vitreous phases, the degree of reactivity between components and the thermal compatibility between glaze and substrate are determining factors in obtaining resistant, durable materials that comply with market quality standards.
Technological innovations to improve resistance
The ceramic sector is evolving rapidly thanks to the introduction of new technologies and formulations aimed at improving performance. Innovations are focused on enhancing mechanical, chemical and thermal resistance to meet the needs of the most demanding applications.
Additives and functional materials for improving mechanical properties
The integration of functional additives into enamel and coating formulations is an effective strategy for improving performance. Among the most widely used solutions in the sector are:
- use of high-hardness grits to reinforce the glazed surface
- optimisation of grain size distribution to increase density and reduce porosity
- introduction of stable matting agents to reinforce surface cohesion
These solutions help increase wear resistance and stability in chemically aggressive environments or those subject to frequent mechanical stress.
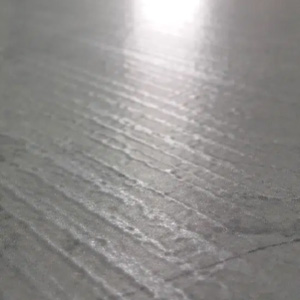
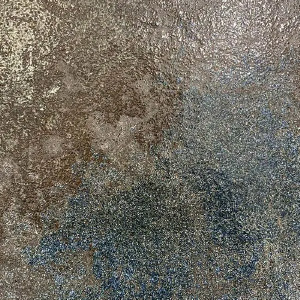
Advanced surface treatment technologies
In addition to composition, surface performance can also be improved through physical-chemical treatments applied in the final stage of the production process. Common practices include:
- use of self-cleaning or antibacterial glazes through the addition of specific components
- multi-stage firing techniques that optimise the distribution of internal stresses
- improvement of the thermo-mechanical compatibility between the glaze and the substrate
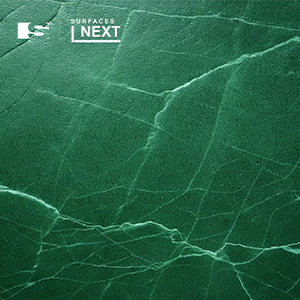
In the case of Sicer’s NEXT EXPERIENCE SURFACES products, innovation lies in the ready-to-use mixture with calibrated microgranules, which allows for even application, excellent cleanability and high resistance to chemicals and abrasion.
Developments in the formulation of high-strength materials
Ceramic research has enabled us to define ad hoc formulations for specific applications, focusing on the following aspects:
- selection of frits with high silica or alumina content
- control of crystallisation of glass phases to improve compactness
- study of thermal cycle behaviour to ensure stability in real conditions of use
The formulations are tested according to the main ISO standards to verify their mechanical, chemical and thermal stability.
Innovative products for specific high-stress applications
Innovation is also expressed through the development of product lines dedicated to high-performance environments, such as:
- high-traffic industrial flooring
- coatings for outdoor use exposed to frost, UV rays and pollutants
- technical surfaces for the healthcare or agri-food sector
These applications require materials that guarantee long-lasting resistance and minimal maintenance, combined with customisable aesthetic characteristics.
Industrial applications and choice of materials
The choice of ceramic materials for industrial use cannot be made without carefully assessing the performance required in relation to the application context. The various forms of resistance – mechanical, chemical, wear and thermal – must be considered during the technical design phase and when specifying the technical requirements.
Selection criteria based on specific resistance requirements
Every environment imposes different conditions, and it is therefore necessary to identify:
- the type of stress expected (traffic, loads, impacts, chemical agents)
- the level of frequency and intensity of exposure
- the applicable reference standards (e.g. ISO 10545, EN 16165)
Based on this information, the correct ceramic system (formulation + treatment + installation) can be selected to guarantee the minimum certifiable resistance and durability over time.
Applications based on the different types of resistance required
Application context | Priority resistance | Example of suitable material |
Industrial environments and logistics | Abrasion, compression | Technical stoneware with textured finish |
Food and healthcare sector | Chemical agents, stains | Glazed vitrified surfaces |
Exterior in cold/humid climates | Frost, thermal shock | Low absorption porcelain stoneware |
High-traffic areas (commercial) | Wear, impact, ease of cleaning | Surfaces with PEI rating 4-5 |
The association between the type of environment and the resistance required is a fundamental step in avoiding premature damage or unexpected maintenance and replacement costs.
Correlation between costs, performance and resistance levels
The design of high-performance surfaces involves a higher initial investment, but ensures a longer life cycle and a reduction in indirect costs. Companies in the construction and industrial sectors are progressively adopting solutions that maximise:
- Certified technical durability
- Programmed wear resistance
- Easy cleaning and sanitising
This vision is consistent with a life cycle cost (LCC) approach focused on the economic sustainability of the investment.
Future trends in the development of high-strength materials
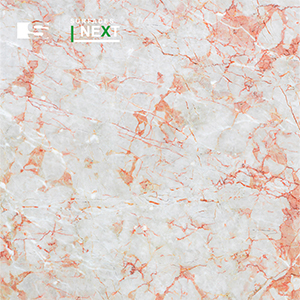
Among the main evolutionary trends in the ceramic sector:
- expansion of the range of high-performance ready-to-use formulations
- introduction of surfaces with integrated functionalities (e.g. anti-slip, self-cleaning, anti-bacterial)
- optimisation of processes to reduce energy consumption and increase thermal efficiency
- increasing focus on the sustainability of raw materials and low environmental impact production cycles
Through constant updating of its solutions and the work of its R&D department, Sicer responds to these challenges by offering advanced materials such as NEXT EXPERIENCE SURFACES, which combine high technical performance with contemporary aesthetics and industrial applicability.
Conclusion
Understanding how ceramic resistance works means knowing how to analyse every aspect of the material: from its composition to its microstructure and surface treatments. Regulatory testing is a fundamental tool for ensuring that products are suitable for their intended use. Solutions such as NEXT EXPERIENCE SURFACES demonstrate how it is possible to combine high performance with ease of use and advanced technical characteristics.
FAQ
It depends on the type of material and the test applied. It is measured according to specific standards (e.g. ISO 10545-4 for bending).
Structural stability, durability, resistance to wear, chemicals and temperature changes. Ceramic tiles are ideal for industrial and commercial applications.
This question refers to electronic components, which are not covered in this article. Here we are talking about the structural strength of ceramics in construction and industry.
NEXT EXPERIENCE SURFACES are opaque, anti-reflective microgranules, ideal for technical surfaces that are easy to clean. GHR granules are designed for high-stress environments: they offer high abrasion resistance and excellent graphic performance. The GRA series is specifically designed for dry applications and mirror lapping, ideal for achieving extremely bright and compact surfaces.
Yes. All grits in the GHR and GRA ranges are tested to ensure resistance to acids (3% and 18% HCl) and aggressive chemical conditions, as reported in the technical tests included in the official product data sheets.
Yes, GHR are suitable for outdoor applications. Their abrasion resistance, transparency and the possibility of creating non-slip surfaces make them ideal for flooring exposed to heavy traffic or atmospheric agents.
GRA grits allow the creation of highly polished lapped surfaces with excellent flatness, scratch resistance and absence of microporosity, thus improving production efficiency and final aesthetic quality.